Six Sigma strategy, key for continuous process improvement
Many methodologies have emerged throughout the history of quality, being a result of a change of their own focus. Some examples are PDCA, 7-step TQC or Teops8D2 and have proven their value but still, Six Sigma is the one that has demonstrated the best results.
History
The strategy was first implemented the end of the 80s by the engineer of Motorola Bill Smith and boosted by General Electric. Bill, guided by his own approach of increasing Motorola’s process performance, put a higher emphasis in the reduction of the variation and the increase of the quality. Changing their business strategy, Motorola achieve to boost its activity and the operational excellence.
In different meetings, Motorola technicians discovered that by controlling variation, the processes would work and could achieve a final result of 3.4 defects per million opportunities: a level of “six sigma”.
Bill Smith used the Six Sigma concept when studying reliability problems and the relationship between the occurrence of defects and the mean time between failures. He discovered that the correlation between the useful life of a product and the number of times that the product had been repaired during its manufacturing process was very high. Thus, he proved that, if a product was defective during its manufacture, the probability that it had other unnoticed defects was very high.
Just pay attention to the data
Motorola achieved an increase in its annual productivity by almost 15%, an annual growth of 17% and the elimination of 99.7% of defects in its processes. The company obtained not online a reduction of the costs but also an increase of its competitiveness in the market. Today, companies from different industries have incorporated this work philosophy into their operations system.
Objective
The main purpose of those companies that implement Six Sigma is to improve their processes, seeking profitability and productivity through the increase of their quality levels. Being a strategy focused on the reduction of the processes’ variability, Six Sigma help businesses to optimize all phases involved and get a reduction of the defects of the product or service that clients finally receive.
The Six Sigma work philosophy is to identify and eliminate all those real causes that prevent or hinder the adjustment of the products to the established invariability requirements.
Improving processes, we will have a much better control of them and will be able to identify when the stablished quality standards are not being fulfilled.
To sum up, the results attained are the improvement of the products final characteristics and the cost saving. In other words, higher earnings and client’s satisfaction.
Estimate of Six Sigma
Six Sigma is based on statistical tools and techniques, such as Statistical Process Control, SPC. It is calculated very similarly to the Process Capability Index, PCA. In this case, the value obtained is the number of standard deviations that fall within the specification limits. It is assumed -one controversies of the methodology itself – that 1.5 units must be subtracted from the sigma calculated in sort term to reflect the variability of the process in the long term.
A process whose sigma is equal to six indicates that 3.4 DPMO (Deffects Per Million of Opportunities) are ocurring
In Tests&Trials, the specification limits are the Voice of the Customer (VoC). We know that a process under control may not always meet the specifications, and yet a process that is not under control might be capable of doing so. For this first situation, we can respond by carrying out specific improvement projects that allow to reduce variability. For the latter, we detect and eliminate the special events that cause variation in order to avoid that in the long term this specifications will not be met in the long term.
DMAIC
The Six Sigma basis is DMAIC strategy: Define, Measure, Analyze, Improve and Control. It is a sequential cycle where the different phases are contemplated:
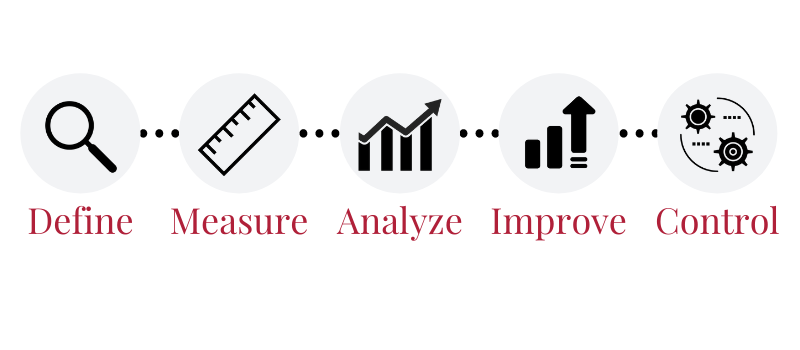
Define: Before change, it is highly important to find out what is failing to improve it and to evaluate the results. In this phase, the problem or defect is identified and the objectives and team that will take responsibility of the process are established.
Measure: What else do we need to know? This question is answered by understanding the current operation and doing an evaluation of the process. Clients requirements, product characteristics and parameters that influence the process performance are identified. After collecting the data, it is determined its reliability and defined the measurement system.
Analyze: The root of the problem or defect is identified. The team seek the real causes that generates variation. After that and by contrasting cause-effect hypotheses with the most related statistical tools, the team determine the variables that will most contribute to the output results.
Improve: Where you get the fun. This is the most creative stage of the DMAIC because is where all ideas or solutions that seem to be feasible are tested before their implementation. With a focus on eliminating waste, this phase does not rely on statistical analysis but on team’s capability.
Control: Measures are taken to guarantee the continuous process improvement and to ensure that the changes are sustainable. There is also a evaluation in terms of cost and client’s satisfaction.
Belts in Six Sigma
This methodology demands the commitment of all the team, either in strategy or operative scope. There are three important roles that, according to their responsibility and knowledge, they are distinguished by a colored belt, alluding to the levels of the martial arts.
Firstly, the Black Belts are the ones who coordinate and direct the Six Sigma projects. They are also responsible of the continuous communication with the direction of the business. They have an advanced knowledge in analytics and tools and have abilities for leadership and problem resolution.
The Green Belts professionals have an intermediate know-how and have all the details of the process. They take careo of the communication of all the basics aspects of the Six Sigma with the rest of the personnel involved. It is their responsability to ensure that all the team is working according to the objectives.
Last but not least, the Yellow Belts. This position is represented by the rest of the staff within the business that participate in the project and have a more basic knowledge of the methodology.
Tests&Trials make use of this success strategy in its philosophy of action to comply with the quality standards that our clients need. Therefore, we achieve a proactive approach in the process and a reduction of waste.
Shall you need our statistics service to boost your performance results, do not hesitate to get in touch with us by calling, sending an e-mail to info@testsandtrials.com or leaving us a message in the website. We will be pleased to help you out.
This work is licensed under a Creative Commons Attribution-NonCommercial-NoDerivatives 4.0 International License.